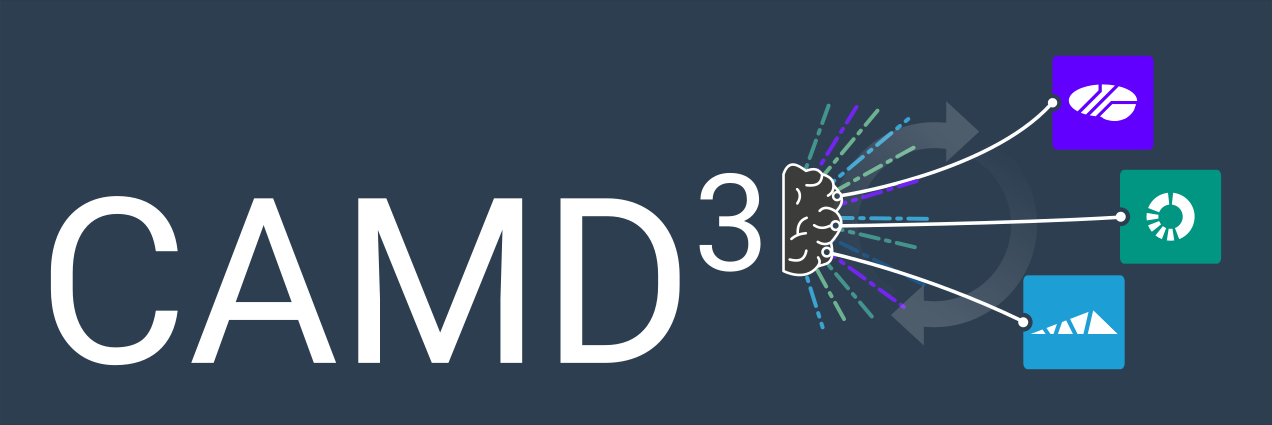
CAMD3D stands for Computer Aided Materials Design 3D, a framework for the accelerated design of novel materials.
The goal of CAMD3D is to combine the capabilities of multiple software solutions to provide an ecosystem for the accelerated development of novel materials. The used software includes Kadi4Mat, a research data infrastructure, PACE3D, a phasefield simulation framework and CIDS, a machine learning library compatible with the aforementioned software systems.
About
CAMD3D is a unique digital platform that combines comprehensive structure generation algorithms with simulation methods based on physical material models for shape and topology optimisation taking into account multi-physical requirements for the newly created materials, and adaptive candidate selection using modern data science applications including machine learning and artificial intelligence methods. This combination enables accelerated virtual material development of cellular materials for the first time. The digital development process and the created property-optimised materials contribute to sustainable production and use with the material- and energy-saving realisation. Based on a broad material science knowledge of microstructural parameters and properties, a virtual framework for accelerated material development was created in the cross-university research group of the Institute for Digital Materials Research (IDM) at Karlsruhe University of Applied Sciences and the Institute for Applied Materials (IAM) at KIT.
Gyroid Structures
Gyroid structures belong to the family of triply periodic minimal surface (TPMS) structures. These algorithmically generateble structures can be both created and simulated in Pace3D. A current focus is the use of the gyroid structure as a potential candidate for a resorbable bone implant structure. In this project, the focus is on shape and topology optimization of such structures to achieve load-specific strength while maintaining or reducing weight. Using CAMD3D, these optimisations are performed while simultaneously modelling and documenting the research process in a holistic and reproducible way.
Porous Structures
In order to accelerate the development of porous microstructures namely polyurethane foams that are used in lightweight applications, the CAMD3D framework is used. The goal of this use case is to predict the mechanical properties of foam structures directly from their microstructural composition. Starting from CT-images of the foams' microstructure, digital twins are reconstructed and analysed using the PACE3D framework. Based on the obtained microstructural properties of the reconstructed foams, further digital models of foam structures are synthetically generated using a specifically designed algortihm. Using a homogenisation approach implemented in PACE3D, the mechanical properties of the foam structures are subsequently simulated. Finally a machine learning approach is trained using the CIDS framework, that establishes a linkage between a foam's microstructure and its effective mechanical properties. To model the complete development process in a FAIR manner, all intermediate data are stored in Kadi4Mat. Additionally, all processes are modelled in form of workflows and added to Kadi4Mat.
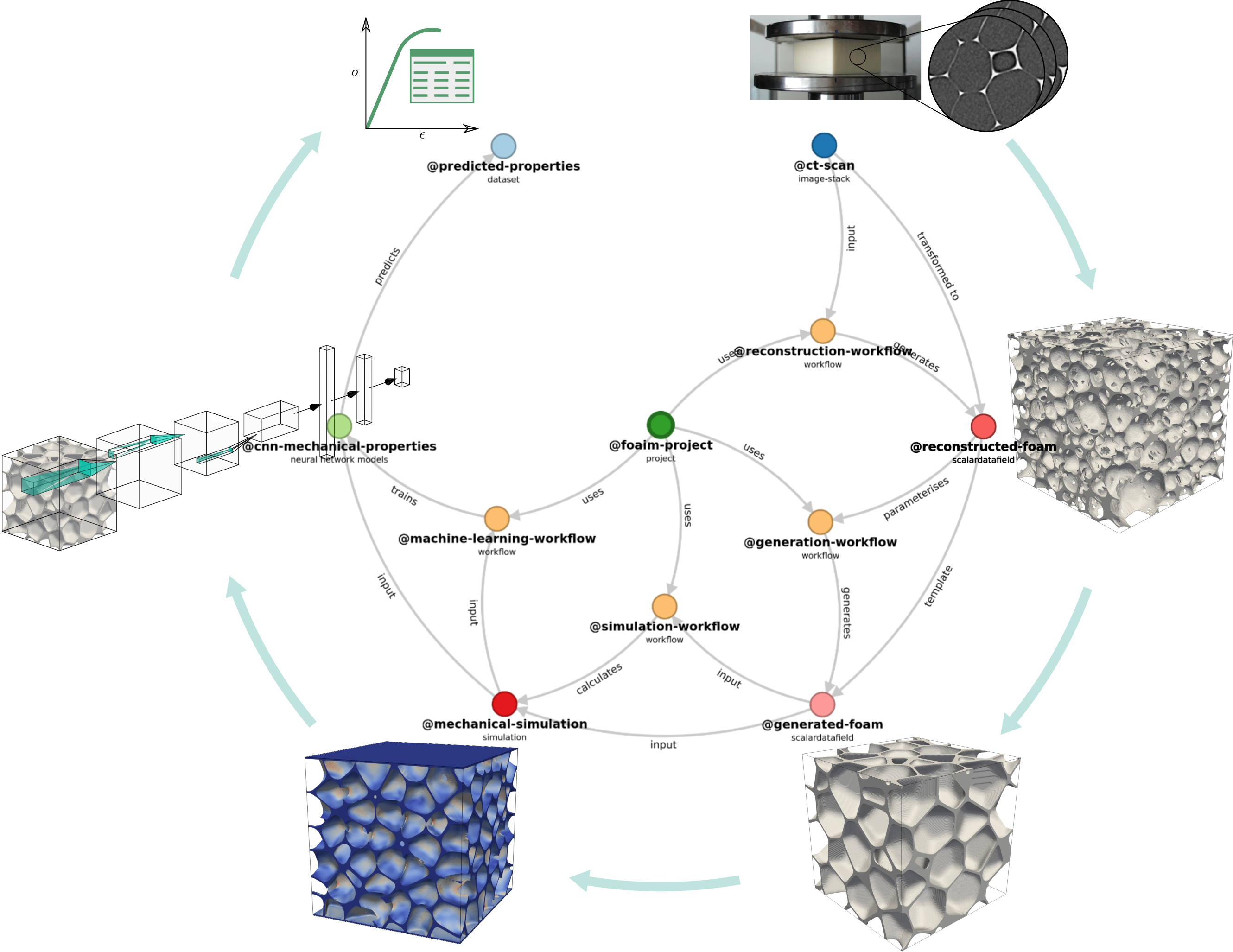
Battery Research
For the development of novel batteries the targeted investigation of different battery materials is necessary. In cooperation with research partners across different disciplines CAMD3D is used for this research. Experimentators use Kadi4Mat to upload and store data obtained from real world samples. This data is subsequently used to parameterise simulation studies as well as to digitally reconstruct the battery structures. Using automatable workflows in Kadi4Mat the reconstruction of battery strucutres is accelerated. Based on the data collected in Kadi4Mat, the CIDS framework can be used to train machine learning approaches, that explore possible microstructures in a targeted fashion, ultimately facilitating the discovery of new battery materials.